Activation Plant for Activated Carbon Production
At Guanbaolin Carbon Industry Group Co., Ltd., we specialize in transforming a diverse range of raw materials into high-quality activated carbon, utilizing our state-of-the-art activation plant(Carbon Activation Kiln). Our advanced facility is designed to process a variety of organic sources, including coconut husk, apricot kernel shell, walnut shell, hawthorn kernel shell, peach kernel shell, coal, and palm kernel shell, to produce superior activated carbon.
Our activation plant harnesses cutting-edge technology and precise control mechanisms to ensure optimal conditions for the carbonization and activation processes. By meticulously managing the temperature, gas flow, and other critical parameters, we achieve the highest levels of efficiency and effectiveness in producing activated carbon with exceptional adsorption properties.
Carbon Activation Kiln
activation kiln is the core of activation process and plays the role of activating material
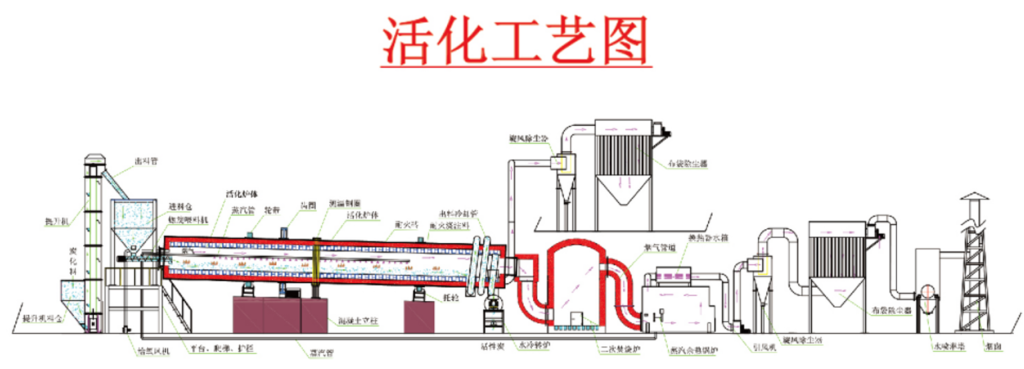
An activation plant for activated carbon production is a specialized facility that utilizes advanced active carbon equipment to convert carbon-rich materials into activated carbon. The process involves carbonization (heating materials without oxygen) and activation (creating pores with steam or chemicals). Essential active carbon equipment includes kilns, furnaces, reactors, cooling systems, and screening machines. This results in high-quality activated carbon used for purification and filtration.
Models | Capacity(t/d) | Heat exhaustion |
---|---|---|
1.9m * 10m | 8-10 | Self-balancing of material without thermal energy |
2.2m * 10m | 13-16 | |
2.6m * 10m | 18-15 |
Active Carbon Equipment Activation Process
An activation plant for activated carbon production is a specialized facility that utilizes advanced active carbon equipment to convert carbon-rich materials into activated carbon. The process involves carbonization (heating materials without oxygen) and activation (creating pores with steam or chemicals). Essential active carbon equipment includes kilns, furnaces, reactors, cooling systems, and screening machines. This results in high-quality activated carbon used for purification and filtration.
Carbon Activation Kiln Gallery
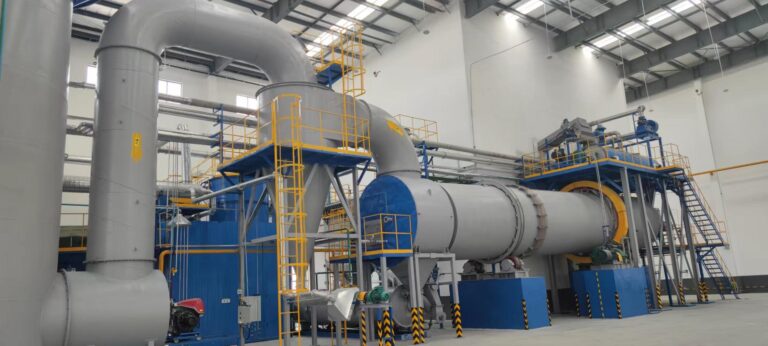
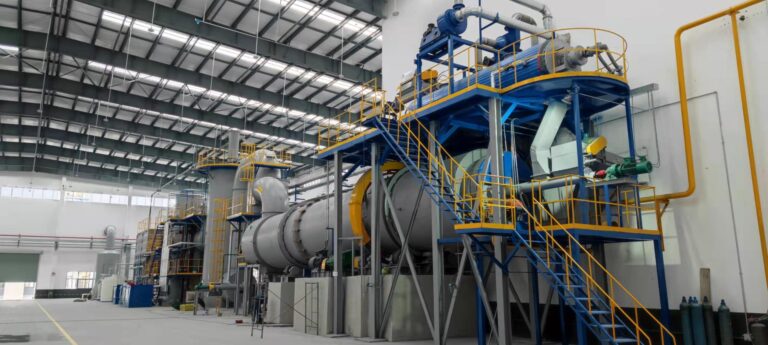
Activation Equipment Parameter
Name | Parameter | Name | Parameter |
---|---|---|---|
Materials | Hard wood material | Induced draft fan | Power: 20KW, air volume of 20000 ㎡/h, wind pressure: 1300MP |
Carbonized material | Moisture <1%, particle size: 1-10cm, ash content <5% | Feed way | Hoist or screw feeder |
Activated carbon | Iodine value > 1100mg/g Methylene blue > 10ml/0.1g |
Carbonization conditions | Saturated superheated steam + high temperature + penetration activation |
Gas composition | Water, carbon dioxide, and carbohydrates | / | |
Out-feeding temperature | 360-400℃ | Dusting method | Cyclone collector, bag filter, spray device |
Temperature behind the cooler | <50℃ | Cooling method | Converter natural cooling tube, external cooling water bath converter |
Power | <100kw | Equipment material | Q345 |
Quantity of steam | 1.5-3t/h | Refractory materials | Steel fiber reinforced castable, high alumina refractory brick |
Steam pressure | 6kg | Insulation thickness | >40cm |
Steam flow | 1.5-2.5t/h | Aluminum content of resistant material | >45% |
Flue gas temperature at inlet | 800-950℃ | Maximum temperature of resistant material | >1300℃ |
Furnace temperature | 850-1050℃ | Gas amount | 10,000 m3/h |
Flue gas incinerator temperature | 800-950℃ | Temperature sensing thermocouple | Unit: 3, Heat-resistant: 1200℃ |