Internal Thermal Biomass Carbonization Plant
Activated carbon production through biomass carbonization or biochar production involves heating biomass under limited oxygen or completely oxygen-free conditions to undergo slow decomposition. This process releases volatile components and produces solid biochar, which is a key step in the activated carbon manufacturing process. In addition to biochar, combustible gases, and wood vinegar are also generated. The main by-product of carbonization is biochar, which is both green and environment-friendly, essential for producing activated carbon.
How does biomass carbonization turn waste into wealth?
How does biomass carbonization turn waste into wealth? The biomass carbonization plant is the best way to make money with the carbonization process, ultimately contributing to the production of activated carbon. The activated carbon generated can be utilized in various industrial applications, making this process efficient and environmentally friendly.

Active Carbon Equipment Activation Process
A biomass carbonization plant is engineered to produce activated carbon and charcoal from diverse materials such as wood chips, sawdust, bamboo, and coconut shells. Guanbaolin, a professional rotary kiln supplier, offers customized solutions for biomass carbonization, activated carbon plants, regeneration plants, and other fields. Our biomass carbonization plant solutions encompass design, carbonization machine manufacture, installation, debugging, and personnel training, focusing on the production of high-quality activated carbon.
The entire biomass carbonization plant is environmentally friendly. All harmful substances are removed, and by-products like biochar, wood vinegar, and combustible gas are recycled and used in other applications. The activated carbon produced is of exceptional quality, making it suitable for various industrial applications. The combustible gas can be directly utilized to heat the biomass carbonization system, enhancing the efficiency of the activated carbon production process.
Our biomass carbonization plant is more than just a biochar production line; it’s a recycling process. The entire recycling process is a self-heating reaction that provides a positive energy balance. Only the energy generated during the waste carbonization process is needed to drive the equipment. The generated heat energy can be used on-site or connected to the local heating network, ensuring a sustainable and efficient activated carbon manufacturing process.
Biomass Carbonization Solution
Waste Heat Utilization System
Models | EUBC-100 | EUBC-300 | EUBC-500 | EUBC-1000 |
Fuel Performance (MWth) |
1.67 | 5 | 8.4 | 16.8 |
Annual Treatment Volume of Biomass (tons/year) |
3*10 | 9*103 | 1.5*104 | 3*104 |
Biochar Output (kg/h) | 100 | 300 | 500 | 1000 |
Annual Biochar Output (tons/year) |
750~900 | 2250~2700 | 3750~4500 | 7500~9000 |
Heat Output (MWth) | 0.5 | 1.5 | 2.5 | 5 |
Annual Working Hours (h) |
7500 | 7500 | 7500 | 7500 |
Footprint (m²) | 85 | 100 | 140 | 190 |
Quantity of Containers (L*W*H)(mm) |
9000*2350*2700, 1pcs 6000*2350*2700, 2pcs |
9000*2350*2700, 2pcs 6000*2350*2700, 1pcs |
12000*2350*2700, 2pcs 6000*2350*2700, 1pcs |
12000*2350*2700, 4pcs 6000*2350*2700, 1pcs |
Waste Heat Drying System
Models | EUBC-100 | EUBC-300 | EUBC-500 | EUBC-1000 |
Fuel Performance (MWth) |
1.67 | 5 | 8.4 | 16.8 |
Annual Treatment Volume of Biomass (tons/year) |
3*10 | 9*103 | 1.5*104 | 3*104 |
Biochar Output (kg/h) | 100 | 300 | 500 | 1000 |
Annual Biochar Output (tons/year) |
750~900 | 2250~2700 | 3750~4500 | 7500~9000 |
Heat Output (MWth) | 0.46 | 1.39 | 2.32 | 4.64 |
Annual Working Hours (h) |
7500 | 7500 | 7500 | 7500 |
Footprint (m²) | 90 | 110 | 150 | 200 |
Quantity of Containers (L*W*H)(mm) |
9000*2350*2700, 1pcs 6000*2350*2700, 1pcs |
9000*2350*2700, 2pcs 9000*2350*2700, 1pcs |
12000*2350*2700, 2pcs 9000*2350*2700, 1pcs |
12000*2350*2700, 3pcs 9000*2350*2700, 1pcs |
Cracking Power Generation System
Name | EUBC-100 | EUBC-300 | EUBC-500 | EUBC-1000 | |
Carbonization Furnace |
Fuel Performance (MWth) | 1.67 | 5 | 8.4 | 16.8 |
Annual Treatment Volume of Biomass (tons/year) |
3*103 | 9*103 | 1.5*104 | 3*104 | |
Biochar Output (kg/h) | 100 | 300 | 500 | 1000 | |
Annual Biochar Output (tons/year) | 750~900 | 2250~2700 | 3750~4500 | 7500~9000 | |
Heat and Power Output |
Power Generation Capacity (MWe/h) | 0.22 | 0.65 | 1.08 | 2.16 |
Heat Output (Tail gas + Circulating water) (MWt/h) |
0.65 | 1.3 | 2.16 | 4.32 | |
Gasifier | Heating Capacity of Gasifier (MWt/h) | 0.33 | 1 | 1.67 | 3.34 |
Feed Capacity of Gasifier (kg/h) | Approx 233 | Approx 700 | Approx 1200 | Approx 2400 | |
Biochar Output from Gasifier (kg/h) | Approx 23 | Approx 70 | Approx 120 | Approx 240 | |
Annual Working Hours (h) | 7500 | 7500 | 7500 | 7500 | |
Footprint (m2) | 400 | 450 | 550 | 700 |
Internal Thermal Biomass Carbonization Gallery
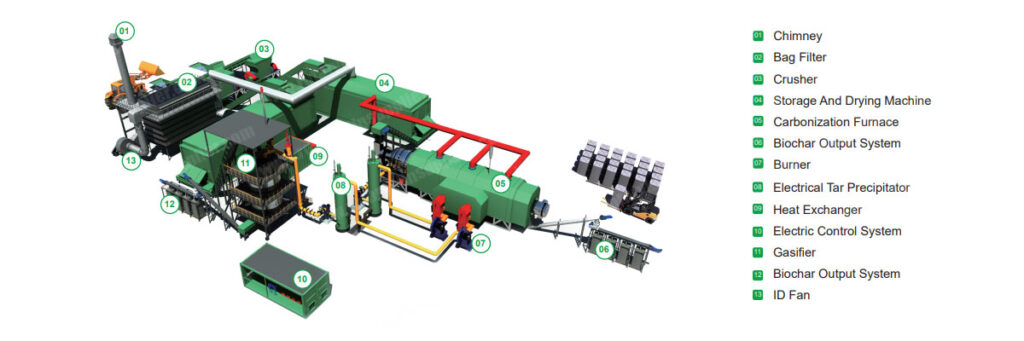
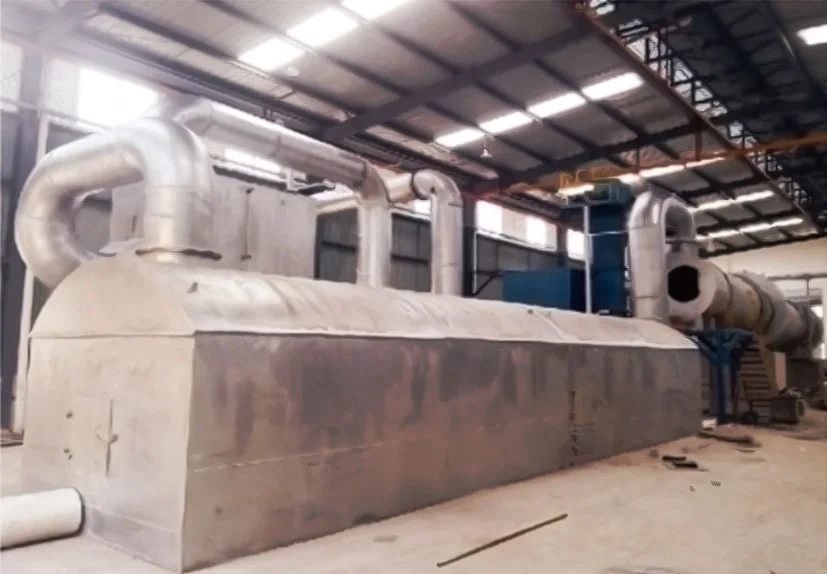
Carbonization process
As we mentioned before, our biomass carbonization process is not an isolated section, it is a new pattern of the recycling economy, we can realize various goals through the biomass carbonization process, reduce carbon emissions, recycle waste materials, produce many by-products, etc.
- The carbonization treatment process is not incineration, but a harmless cracking process (500-800 ℃). All organic harmful substances (such as solvents, plastic particles, lubricants and release agents, drug residues, PFAS, PCBS, PAK, etc.) can be eliminated during the carbonization process.
- Mineral pollutants (mercury, cadmium, etc.) will be separated or inert and will not return to the environment.
- The entire recycling process is a self heating reaction and provides a positive energy balance: only the energy generated during the waste carbonization process needs to drive the equipment.
- The generated heat energy can be used on the project site or connected to the local heating network.
- Reduce waste quantity and cost: up to 95%.